pifpaf
New member
At first glance, it is a bit surprising to see a brand like Concord, with its super-modern designs and its cyberpunk inspirations, featured in our "Savoir Faire and Heritage" summer-school.
But it is the first time I can access such comprehensive information, regarding the production of a watch. Moreover, the creation of a nonconformist watch such as the Black Spider, allows us to put many savoir-faire into perspective.
From the cutting out on numerical control machines to the assembly, through the electroplating and the gemsetting, we will detail the sum of work it takes to produce a Concord C1 BlackSpider Brilliant.
Before discovering the detail of the fabrication process, one should know that this piece is a unique (already sold?).
The titanium case makes 47mm in diameter for 13.55mm in thickness.
The bridge bearing the movement is made of eight distinct parts, and spreads out on the bezel: the "Spider" effect is rather successful, even though it works better on the case-back or on the Blackspider without diamonds.
The gems, fitted on four of the spider's legs, somewhat overshadow the so peculiarly skeletonized movement.
The Blackspider is fitted with a Concepto movement: the C8000 tourbillon is emblematic of their production.
For that matter, the photo of its barrel locking device illustrates the subcontractor's catalog.
The back side of this distinctive piece is unmistakable; on the contrary, the gemsetting on the front side allows the association of the diverse parts to be coherent.
It is quite a bulky movement of 14 lignes 1/4 aka 32.6mm, which is a very suitable size to fill the big watches of the nowadays market. The one-minute tourbillon is set at 21600v/h, with a 72-hour power reserve.
This very open skeleton shows most of the working mechanism, which makes the winding process especially didactic.
One sees the watch living its everyday life; therefore, a power reserve indicator would be absolutely superfluous.
The highlight of this watch is of course the aesthetical link between the bezel and the skeleton. If one could criticize the Concord bezel, one has to admit that when the concept is taken to its limits, the watch reaches another aesthetical dimension.
In order to perfect the look, the inner bezel ring has been machined accordingly.
The other stumbling block of the machining process is the titanium case; as you most certainly know, this metal is particularly difficult to work with: because of its hardness, the high friction can set it to fire.
Therefore, very few brands transform it themselves. Here, the machining of the Blackspider's case takes more than seven hours, with CNC machines specially design to prevent fire hazards.
The bezel is the trickiest part to cut out, as it takes a five axes numerical control machine.
The gemsetting is of course the highlight of this unique piece. As the watch features an almost rough natural element, finding the gems of the right size is a fastidious task.
The next step is the diamonds cleavage; it is like splitting a log. There is a right orientation, with produces two cleanly cut stones. And there is a wrong one, where the diamond will break. If the splitting is properly done, it allows for the elimination of the flaws, which are generally located at the center of the gem.
Then, the diamond undergoes the bruting process, whereby the stone is ground with a diamond mill (of a higher hardness), down to its final shape.
Finally, the most difficult operation, the polishing, where the diamond gets all its facets and its brilliance. This step is performed manually, but of course, the diamond cutter uses a "Dop" (pliers) and a disc turning between 3000 and 4000 revs/min; But surprisingly, he also uses a computer, to guide his movements accurately.
The gems are set using the "grain setting", which is one of the most resistant techniques.
The operation is particularly difficult on the flange, because of the thinness of the material (about 1mm):
Once all the parts are cut out and set, the bridges can be finished. Then, the electroplating is performed. Finally, all the blackened parts are ready to be fitted together.
The previous steps have been properly executed, all the dimensions are perfect. The assembling process is the simplest of all, but at the same time it is the most critical: the task is carefully performed, because if unfortunately a part is scratched or damaged, it must be replaced by a new one.
To produce this C1 Blackspider, set with 224 brilliants, it took a least as many craftsmen and hundreds of hours of work. Because this is the strength of watchmaking: The "Swissness". Many centuries of savoir-faire and unbelievable skills to be able to wear a few tens of grams of happiness.
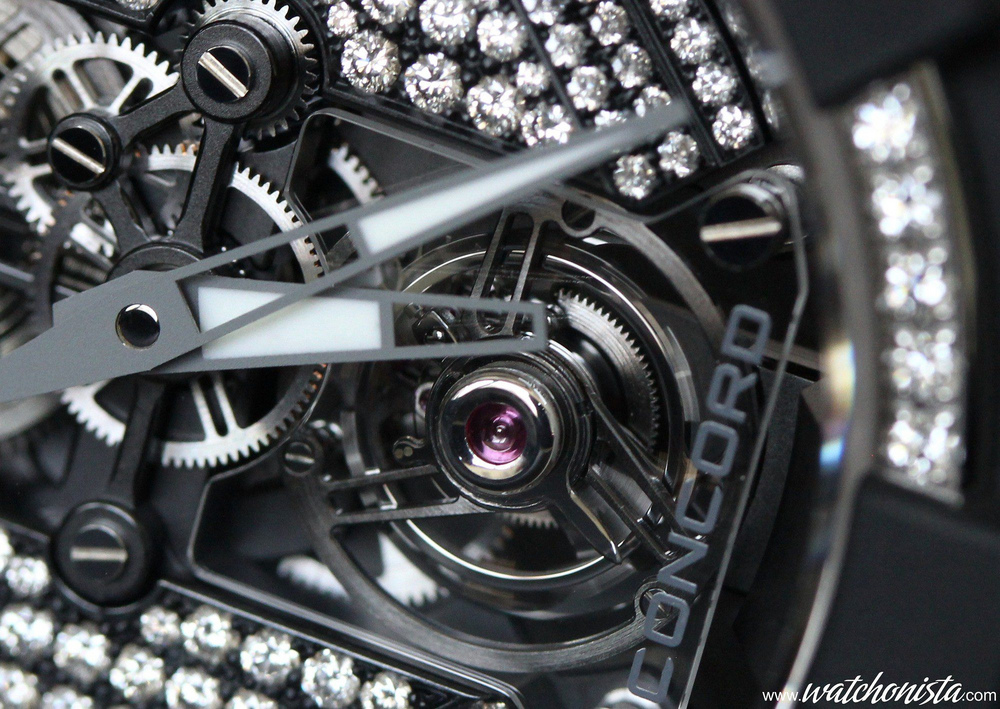
But it is the first time I can access such comprehensive information, regarding the production of a watch. Moreover, the creation of a nonconformist watch such as the Black Spider, allows us to put many savoir-faire into perspective.

From the cutting out on numerical control machines to the assembly, through the electroplating and the gemsetting, we will detail the sum of work it takes to produce a Concord C1 BlackSpider Brilliant.
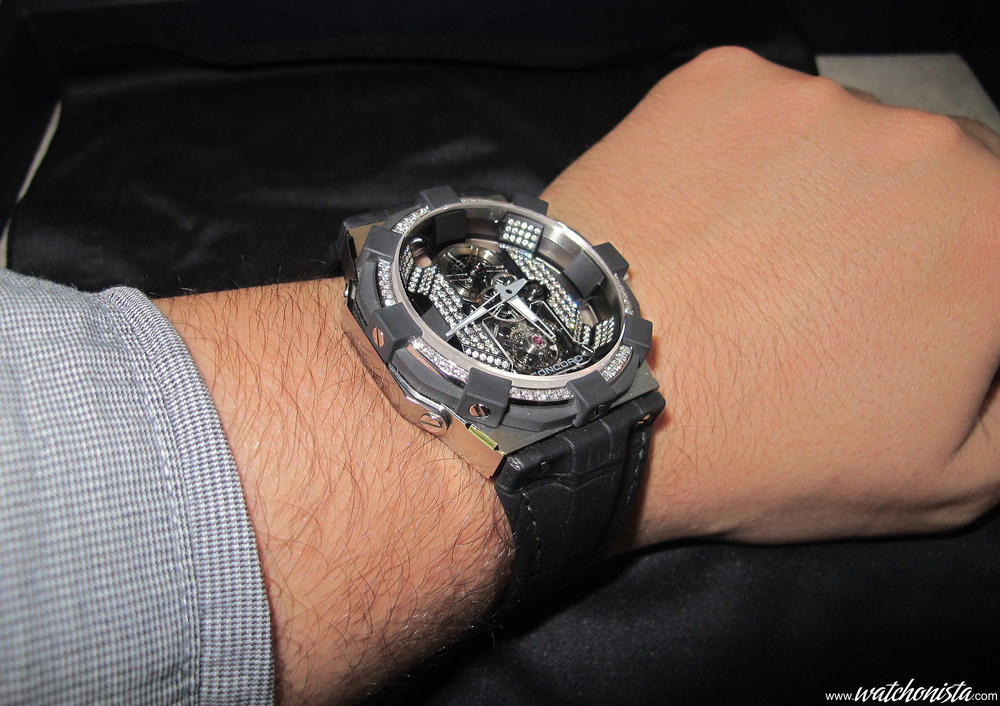
Before discovering the detail of the fabrication process, one should know that this piece is a unique (already sold?).
The titanium case makes 47mm in diameter for 13.55mm in thickness.
The bridge bearing the movement is made of eight distinct parts, and spreads out on the bezel: the "Spider" effect is rather successful, even though it works better on the case-back or on the Blackspider without diamonds.
The gems, fitted on four of the spider's legs, somewhat overshadow the so peculiarly skeletonized movement.

The Blackspider is fitted with a Concepto movement: the C8000 tourbillon is emblematic of their production.
For that matter, the photo of its barrel locking device illustrates the subcontractor's catalog.
The back side of this distinctive piece is unmistakable; on the contrary, the gemsetting on the front side allows the association of the diverse parts to be coherent.
It is quite a bulky movement of 14 lignes 1/4 aka 32.6mm, which is a very suitable size to fill the big watches of the nowadays market. The one-minute tourbillon is set at 21600v/h, with a 72-hour power reserve.
This very open skeleton shows most of the working mechanism, which makes the winding process especially didactic.
One sees the watch living its everyday life; therefore, a power reserve indicator would be absolutely superfluous.

The highlight of this watch is of course the aesthetical link between the bezel and the skeleton. If one could criticize the Concord bezel, one has to admit that when the concept is taken to its limits, the watch reaches another aesthetical dimension.
In order to perfect the look, the inner bezel ring has been machined accordingly.
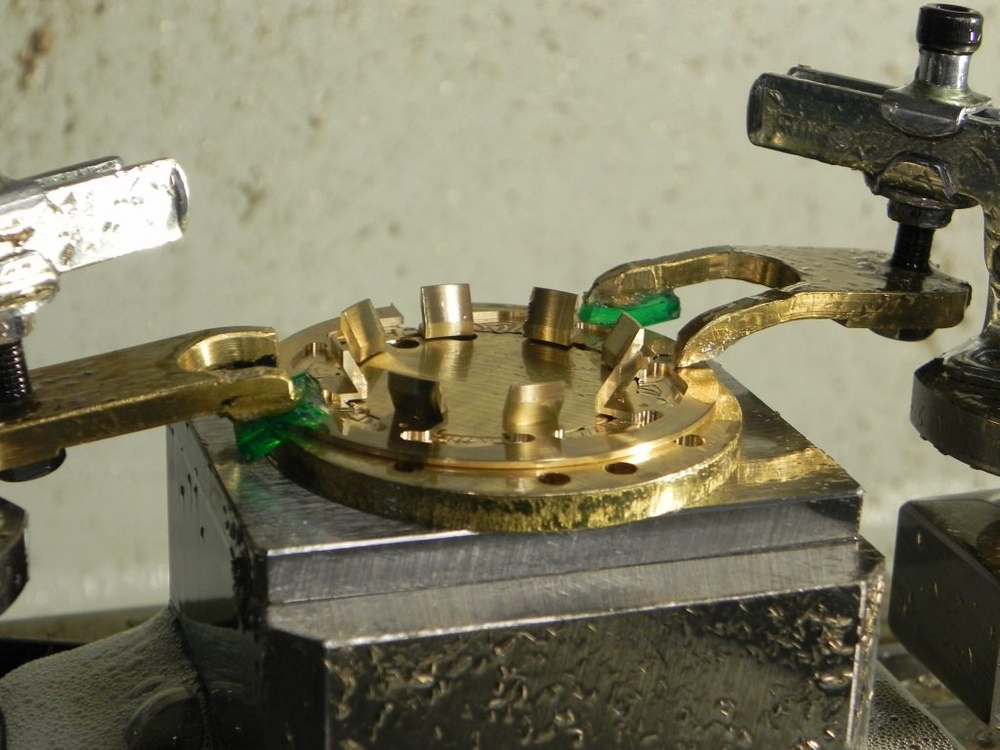
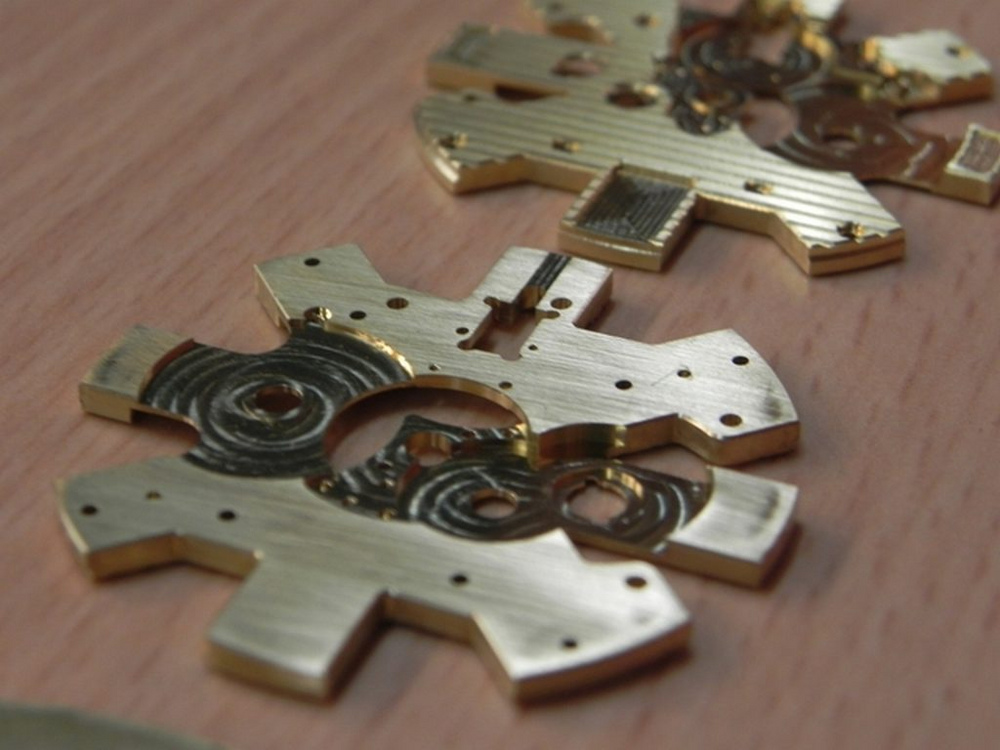
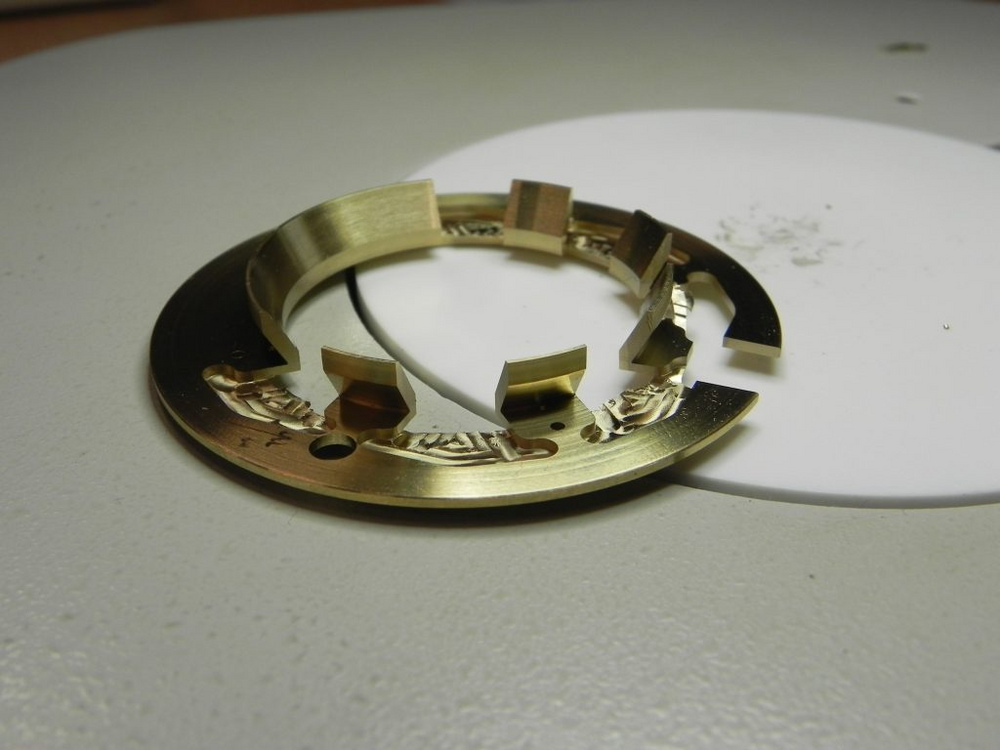

The other stumbling block of the machining process is the titanium case; as you most certainly know, this metal is particularly difficult to work with: because of its hardness, the high friction can set it to fire.
Therefore, very few brands transform it themselves. Here, the machining of the Blackspider's case takes more than seven hours, with CNC machines specially design to prevent fire hazards.
The bezel is the trickiest part to cut out, as it takes a five axes numerical control machine.
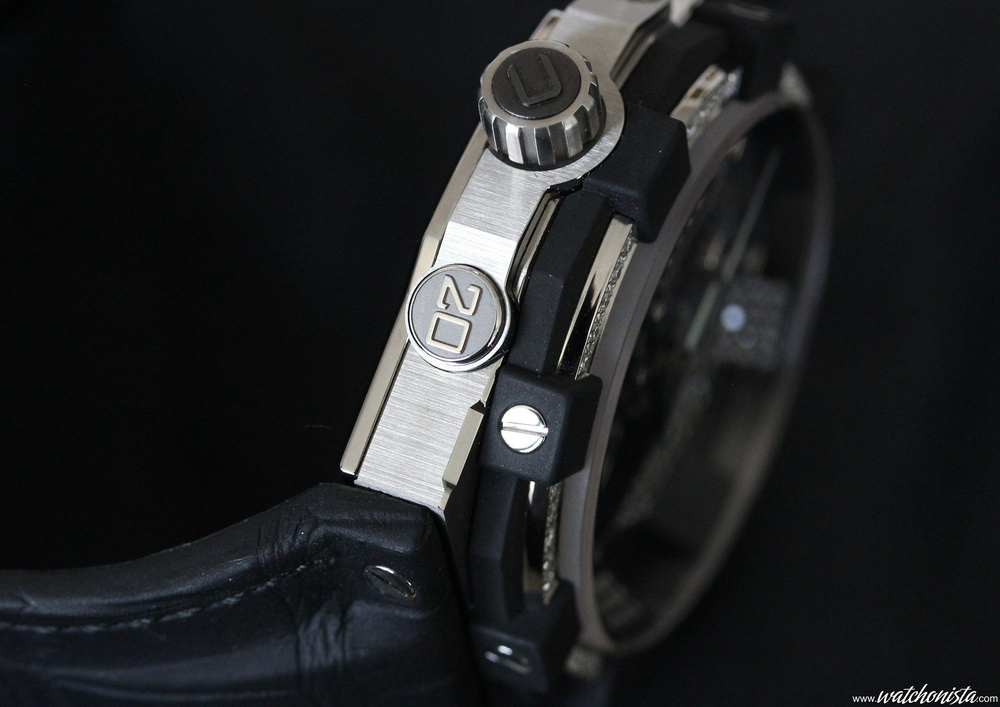
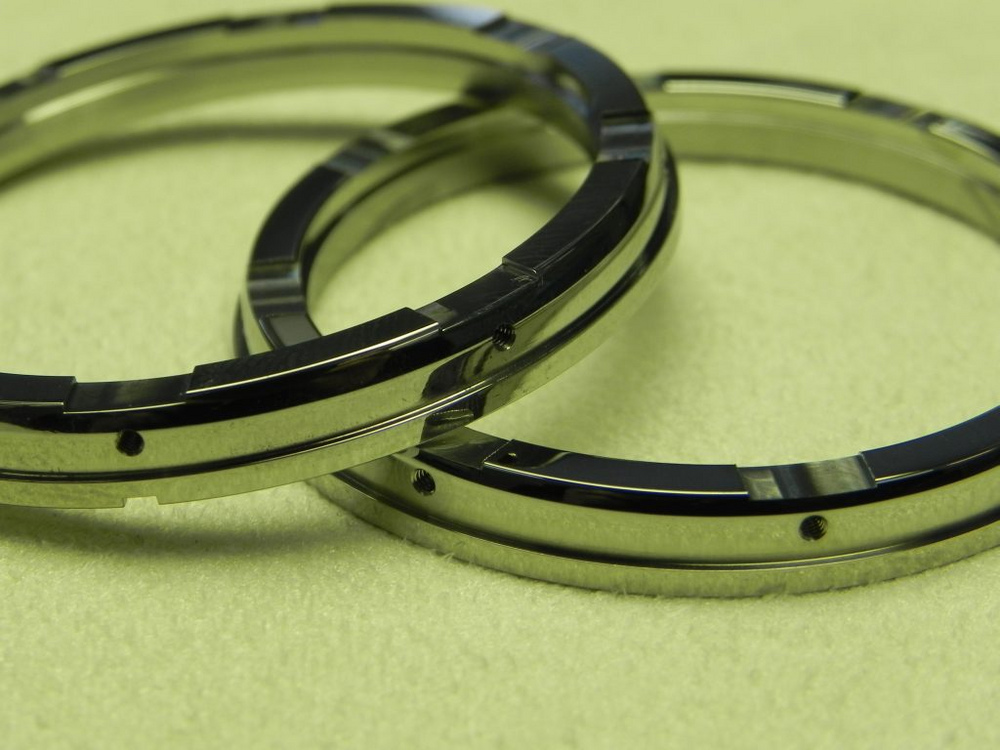
The gemsetting is of course the highlight of this unique piece. As the watch features an almost rough natural element, finding the gems of the right size is a fastidious task.
The next step is the diamonds cleavage; it is like splitting a log. There is a right orientation, with produces two cleanly cut stones. And there is a wrong one, where the diamond will break. If the splitting is properly done, it allows for the elimination of the flaws, which are generally located at the center of the gem.
Then, the diamond undergoes the bruting process, whereby the stone is ground with a diamond mill (of a higher hardness), down to its final shape.
Finally, the most difficult operation, the polishing, where the diamond gets all its facets and its brilliance. This step is performed manually, but of course, the diamond cutter uses a "Dop" (pliers) and a disc turning between 3000 and 4000 revs/min; But surprisingly, he also uses a computer, to guide his movements accurately.
The gems are set using the "grain setting", which is one of the most resistant techniques.
The operation is particularly difficult on the flange, because of the thinness of the material (about 1mm):
Once all the parts are cut out and set, the bridges can be finished. Then, the electroplating is performed. Finally, all the blackened parts are ready to be fitted together.
The previous steps have been properly executed, all the dimensions are perfect. The assembling process is the simplest of all, but at the same time it is the most critical: the task is carefully performed, because if unfortunately a part is scratched or damaged, it must be replaced by a new one.

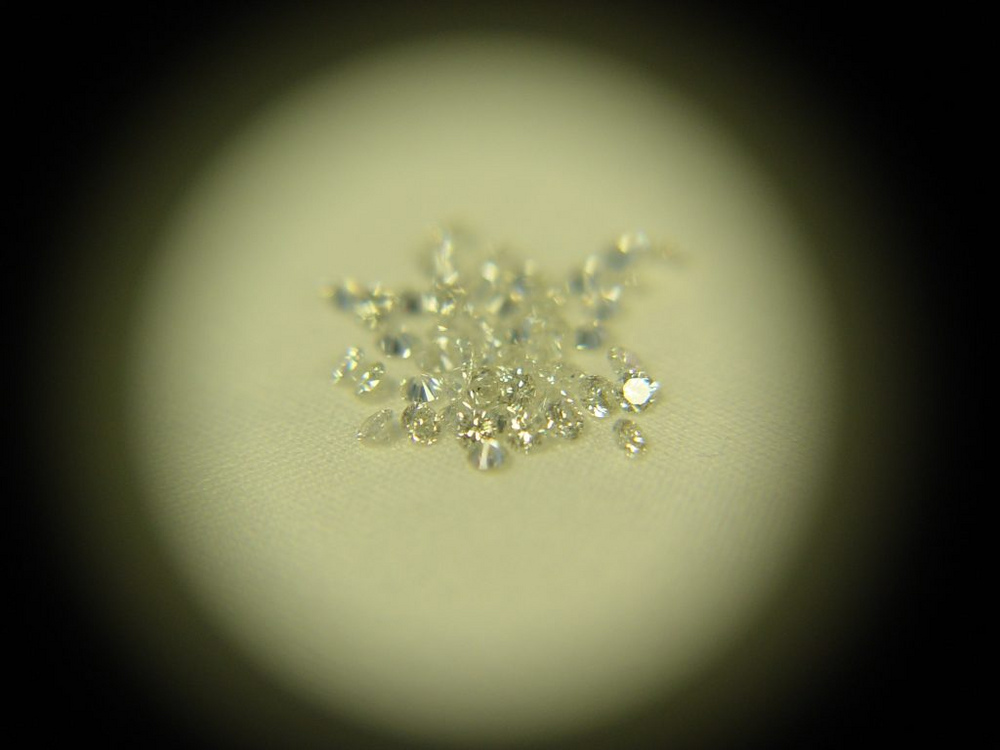

To produce this C1 Blackspider, set with 224 brilliants, it took a least as many craftsmen and hundreds of hours of work. Because this is the strength of watchmaking: The "Swissness". Many centuries of savoir-faire and unbelievable skills to be able to wear a few tens of grams of happiness.


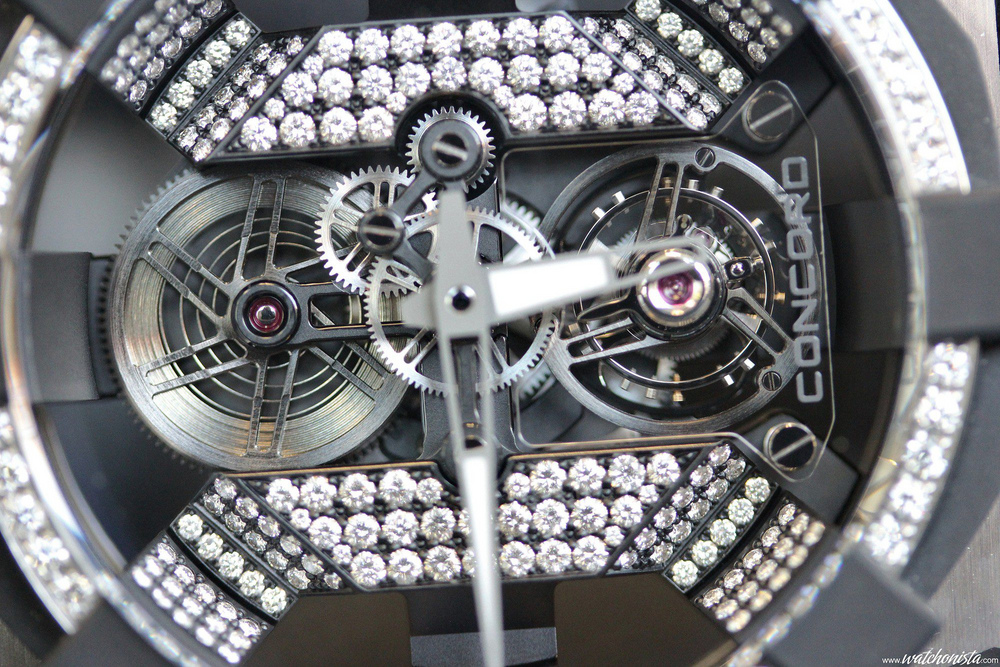